Marine plywood is a great sheet material that can be easily cut using both hand saws and basic power tools. Marine plywood is often used to build boat interiors and to replace flooring during boat renovations. But why do we have to use plywood specifically made for the marine environment and are we wasting our money on expensive ‘marine’ plywood when outdoor grade ply may work just as well?
I’m currently working on an 18ft fibreglass fishing boat that has been totally gutted by the previous owner. The boat is currently a ghostly empty shell with nothing but a loose BMC 1.5 engine. With help, the engine has now been moved to the back of the boat in preparation for the rebuild of the boat’s interior. Although it’s a fibreglass boat, it will still require a plywood floor that will need to be reinforced with fibreglass matting. This is to protect it against the elements and to also form a waterproof structural bond to the hull of the boat. It would be a pretty awful to be in a capsized boat but imagine the floor conking you on the head as well if it wasn’t attached. With this in mind, I took to searching the internet for the solution.
Table of Contents
What makes marine plywood so special?
Whilst planning the renovation of my fishing boat my first thought was; why would I need a marine grade plywood when it is going to be coated in resin+ and fibreglassed when it’s finished? Surely if the wood is not exposed then the material lying underneath doesn’t need to be water resistant?

The main issue with using a non-marine plywood is the eternal problem of time. Given sufficient time and use it may be that the protective fibreglass layer becomes damaged allowing water to permeate the surface and begin to rot the underlying plywood. If the plywood is required structurally then this becomes a messy problem indeed. Your floor will begin to sag and rot through. You lose the strength of the plywood backing over time meaning that the fibreglass is then vulnerable to cracks and structural damage. Unless a large amount of fibreglass matting has been used with a good amount of strength then your floor could potentially fail. In theory and like most things in life the more you spend the better your product will be and the longer it will last.
So why not skip the plywood and just fibreglass?
Fibreglass can easily provide enough strength to support the weight of a person without the use of ply, but the amount of matting needed to create a floor would cost a considerable amount more than simply fibreglassing over plywood.
Without the use of moulds, you will always need a backing or core material to laminate over. This is why marine plywood has been the boat builders choice for many years.
So what are we paying for?
Marine Plywood offers high resistance to water, fungus and damp. It is composed of durable face and core veneers and should be free of voids. Essentially you are paying for the time it will last when exposed to harsh environments. Some ply is guaranteed for 15 and 25 years depending on where and what you purchase. Marine ply uses a waterproof higher grade of glue in between the layers of veneer which also has less imperfections than standard plywood, and is marked with ‘BS 1088’ meaning:
“BS1088 is the British Standard specification for marine plywood that applies to plywood produced with untreated tropical hardwood veneers that have a set level of resistance to fungal attack. The plies are bonded with Weather Boil-Proof (WBP) glue.”
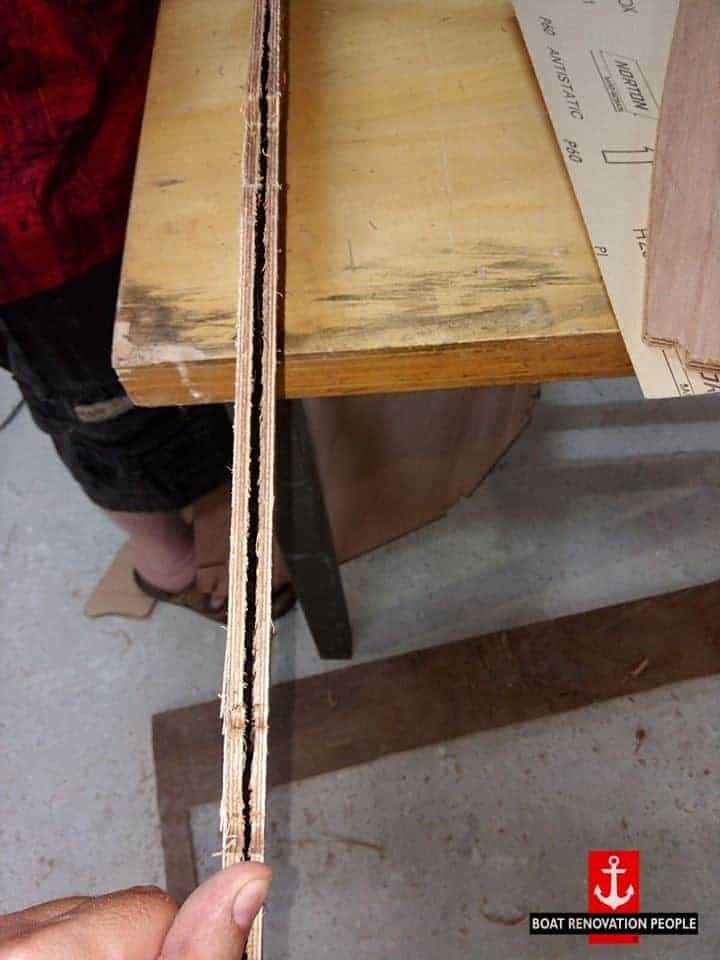
Although this stamp is said to be the seal of approval, there have been various arguments over the years regarding the quality variance. A reader submitted a photo of a piece of so-called ‘marine plywood’ that he recently purchased. It can be seen above the Illustration 1 caption. Don’t worry there are some ways to test the quality of your plywood (at your own risk of course!):
- Cut some small samples and leave them in the dishwasher for a few cycles.
- Simmer samples in hot water for a few days to see if they delaminate.
With these factors now in mind, it is possible to find cheaper alternatives and more importantly available alternatives. It’s all good and well only wanting to use marine plywood but if none of your local building supply store’s sell it, then you won’t get very far!
Exterior grade plywood
Exterior grade plywood is a good alternative to marine ply. Whilst exterior ply may not be pre-sanded and visually free of imperfections, it should still use 100% waterproof glue and should be suitable for permanent exposure to outdoor environments. Exterior ply may also have voids in between the layers that aren’t immediately visible. The only way of truly knowing is by peeling back the layers and inspecting. But all things considered, you shouldn’t go out buying (or building for that matter) without prior research. In the United Kingdom some building suppliers, for example Jewsons, have marine plywood listed on their website. Further investigation however, shows that the marine plywood is in fact not suitable for boat building (their words). Yeh that’s right a product labelled as marine plywood that is not suitable for boat building – like a kitchen knife not suitable for chopping vegetables or a TV that doesn’t show sports! You should always research or run your own tests on a few samples before burning your supplies budget on a bunch of a useless sheet materials.
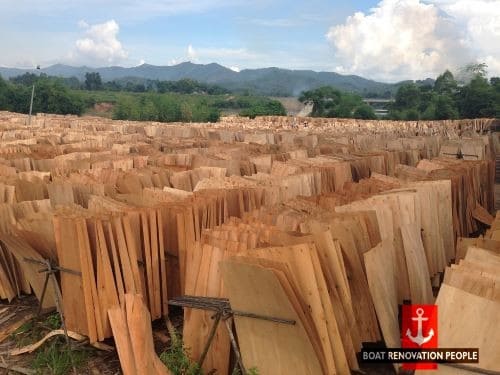
To summarise you should always research or run your own tests on a few samples before burning your supplies budget on a bunch of a poor quality ply sheets. With boat building,you need to get as high a quality as you can afford but make sure its actual quality your buying and not just a name. Don’t think that plywood is poor quality because it comes from abroad, plywood is manufactured all over the world tropical woods being some of the best? Above is a picture of sundried eucalyptus plywood basking in the sun in full glory.
How Marine Plywood Is Manufactured
https://www.youtube.com/watch?v=xGnr8ATHHX8
Photos Of Plywood Delamination And Rot
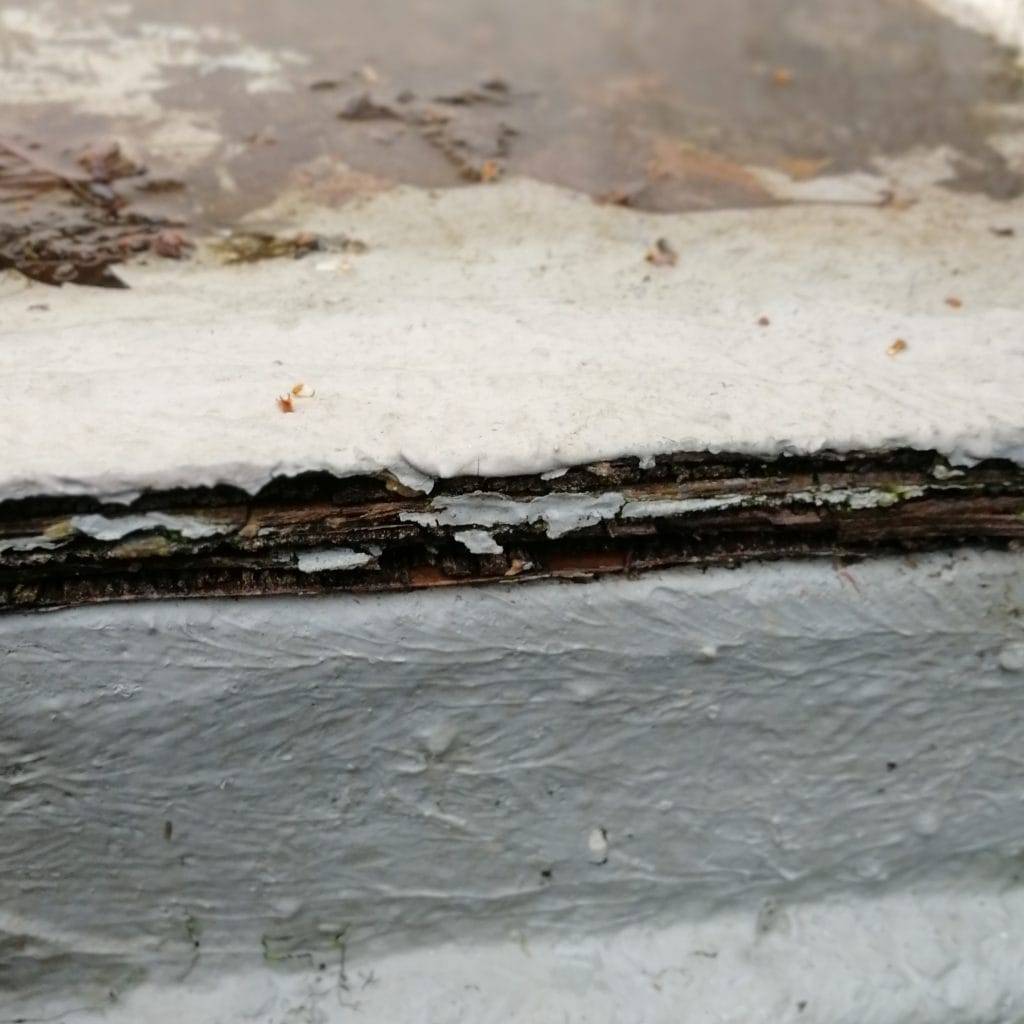
Photo A shows the direct result of not sealing the end of a fibreglass boat deck where it meets the well. The end grain has been exposed meaning water has crept between the plywood and fibreglass over time. The end result is the entire floor is now spongy and most likely rotten. The floor will need to be cut out and replaced.
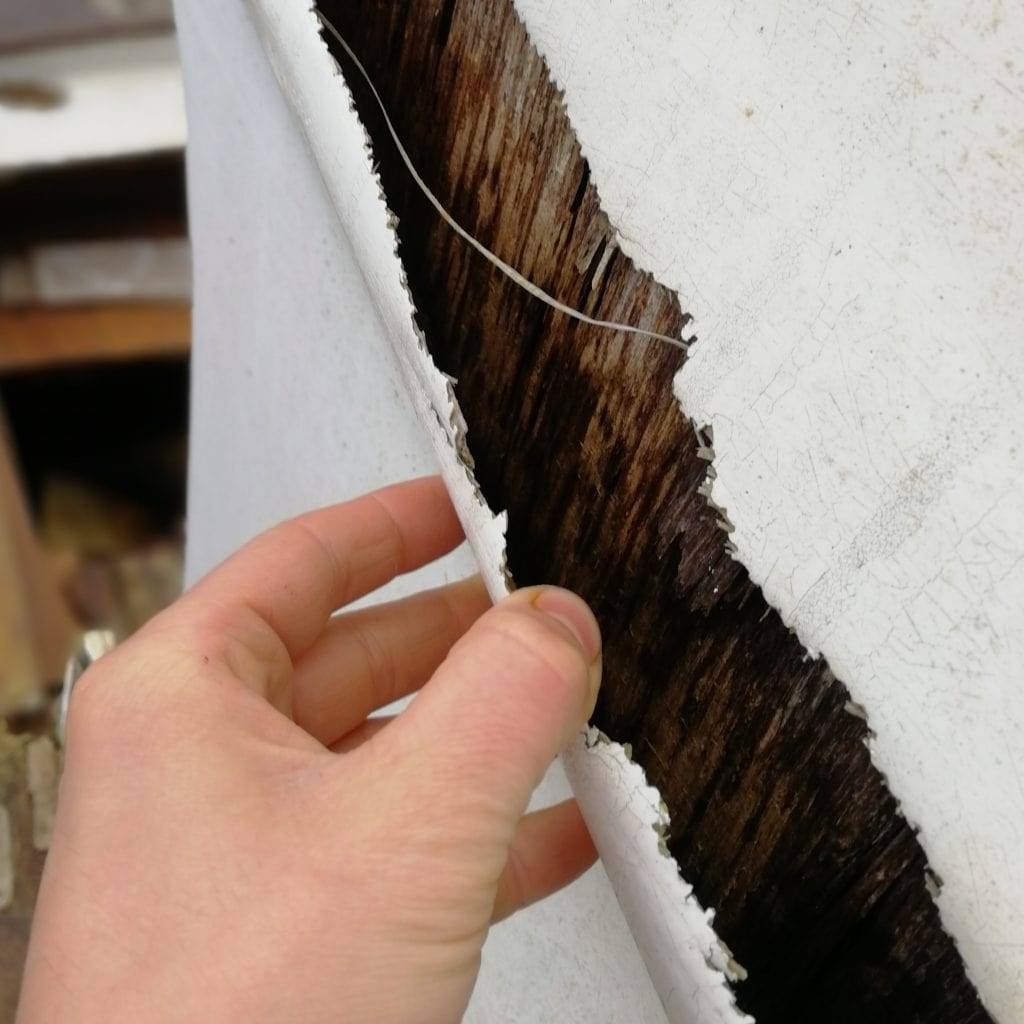
Photo B shows the direct result of water ingress on a plywood cabin side. The top layer of paint is still bonded incredibly well to the plywood but unfortunately the plywood itself has split apart. This may have been caused by a window that sits above this area. Water has got in over time through a poorly window bedded frame.
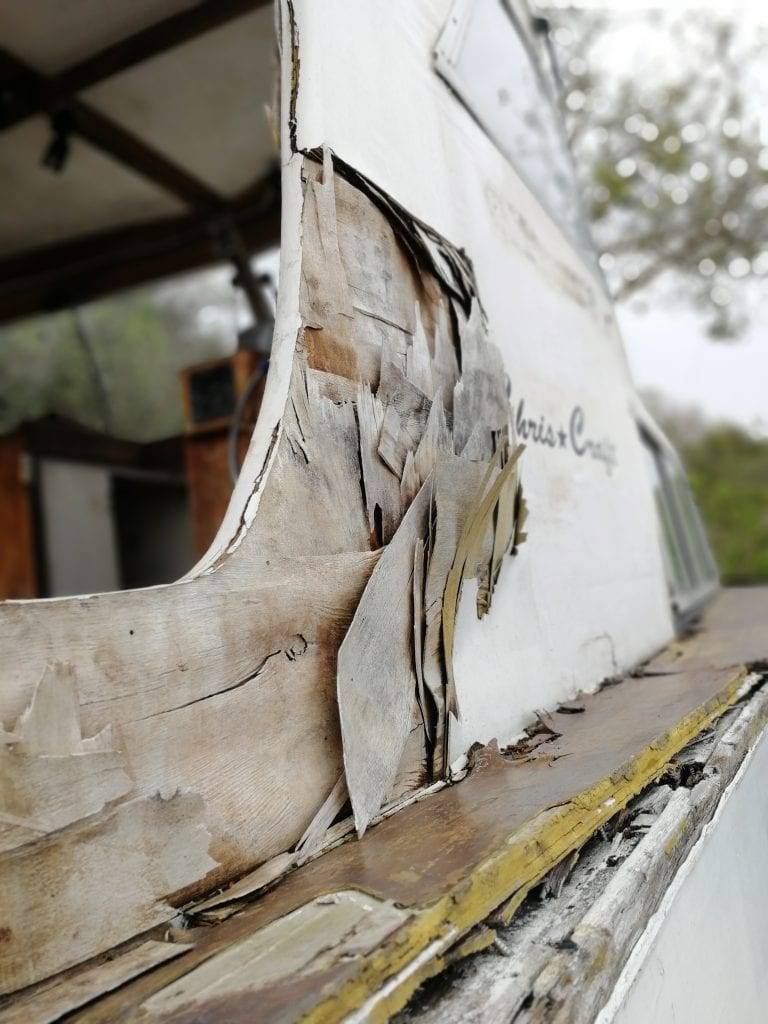
Photo C is a perfect example of plywood delamination at it’s worst. The damage most like occurred where people have been grabbing onto the arch to get onto the boat. Once a crack or break in the substrate occurred water has then been allowed to permeate into the walls. The underlying floor has also been effected majorly.
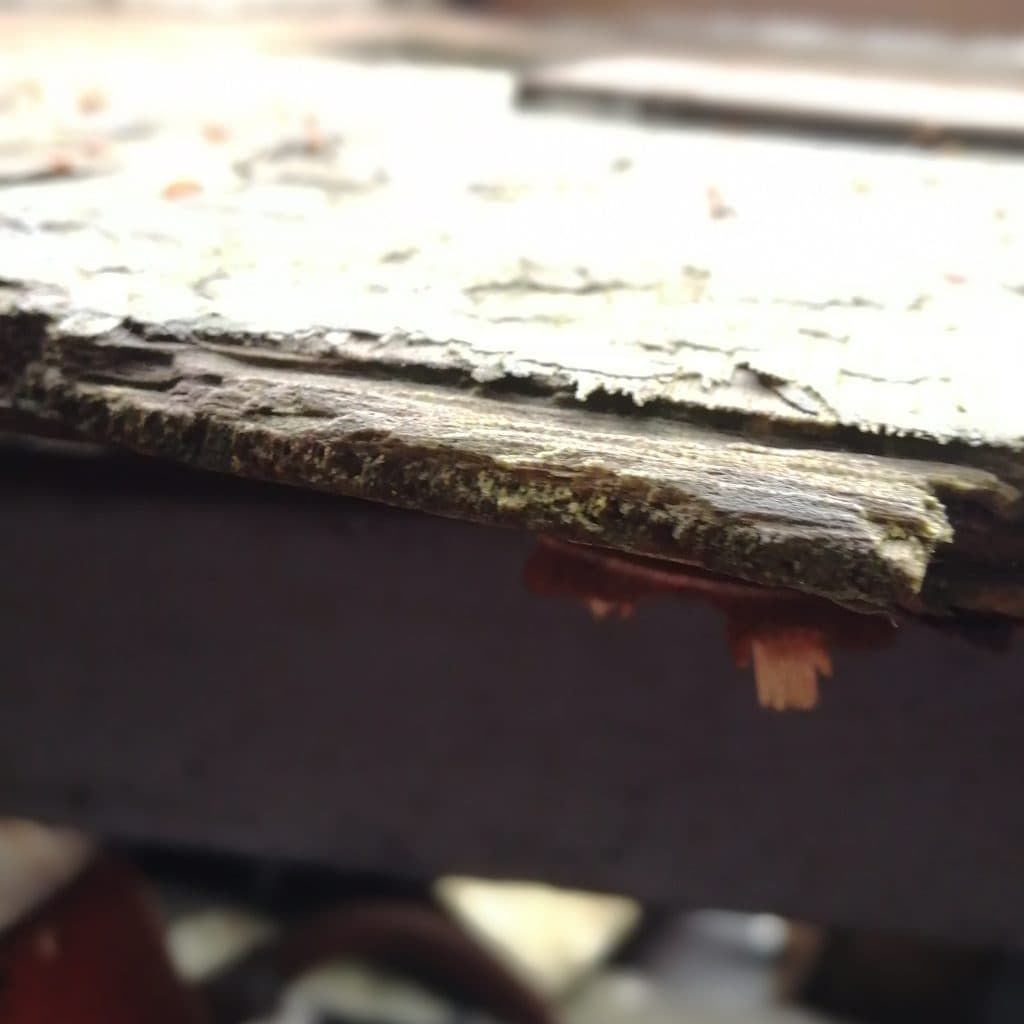
Photo D is a piece of plywood from the floor of a boat wreck. Note that even though the plywood has been snapped and left exposed to rain and wind it still holds its integrity. This was located underneath a faux teak floor meaning that it is most likely the original plywood used to build the floor of the boat. Perhaps this is why it still in better condition than it’s modern counterparts that surround it.
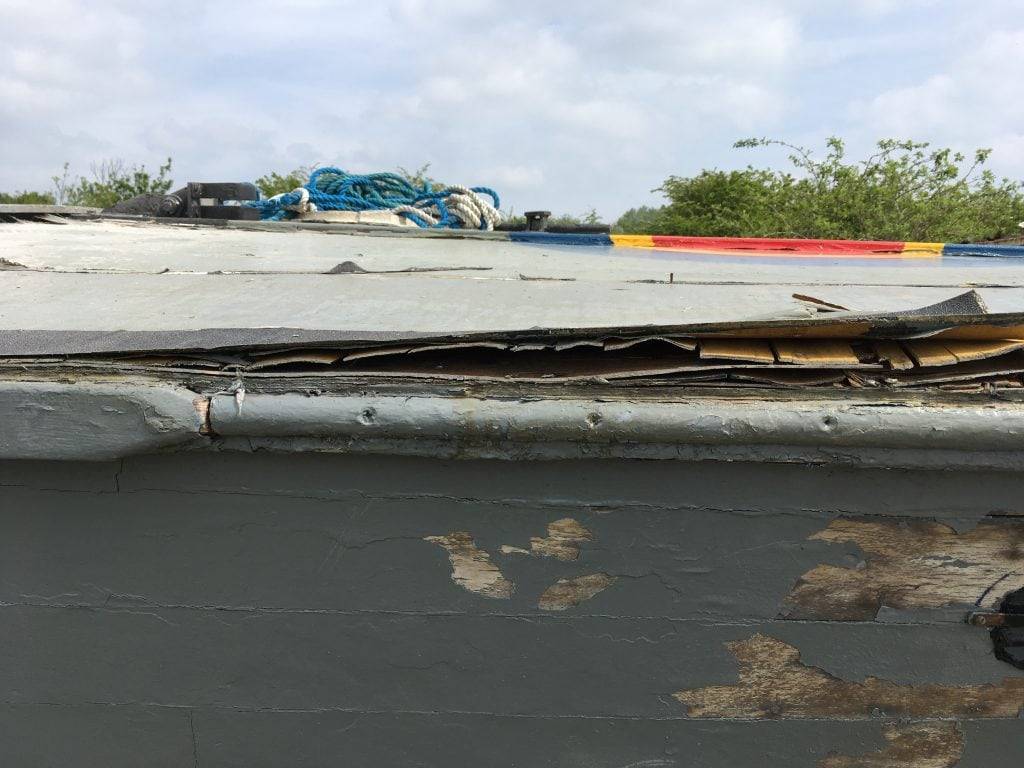
Photo E shows us an example of plywood delaminating even while the boat sits out of the water. The above plywood was labelled as “marine”. This second world war torpedo boat was recently restored , the ends of the plywood were sealed but the water still permeated into the floor causing it to rot. The result is a floor that feels spongy to touch.
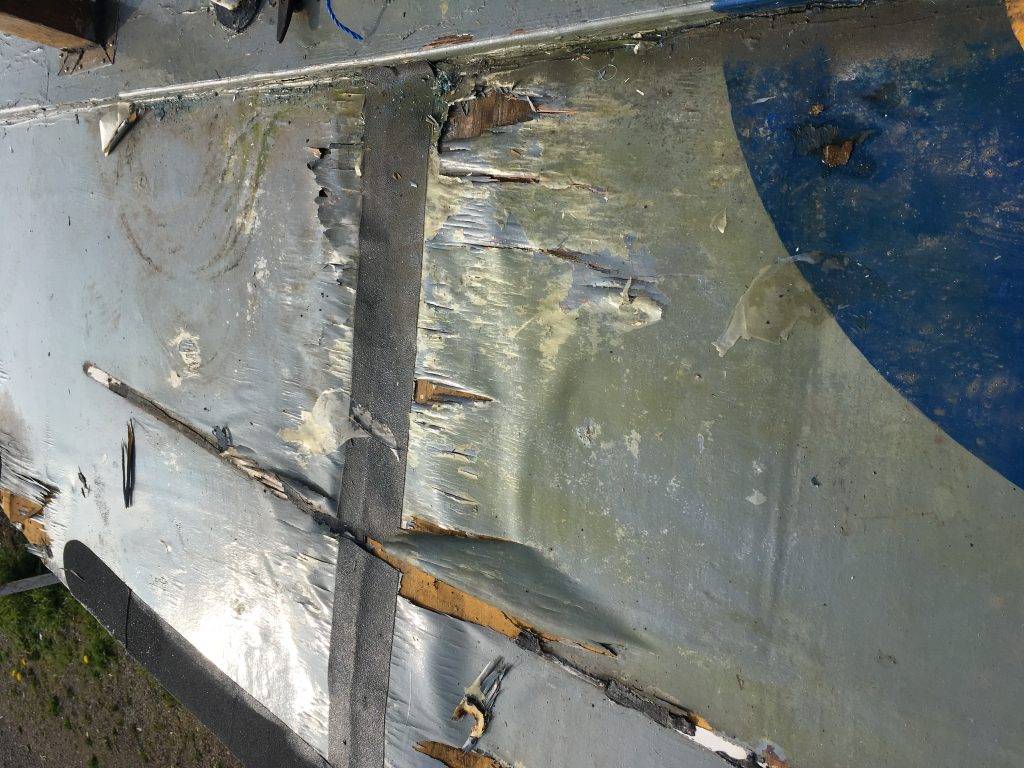
In Photograph F above we can see that the underlying plywood has started to delaminate. The paint is completely failing to adhere to the plywood substrate and subsequently peeling off. Once water is allowed to permeate the plywood it begins to rot. This causes the paint to flake off in large chunks, along with layers of rotten ply.
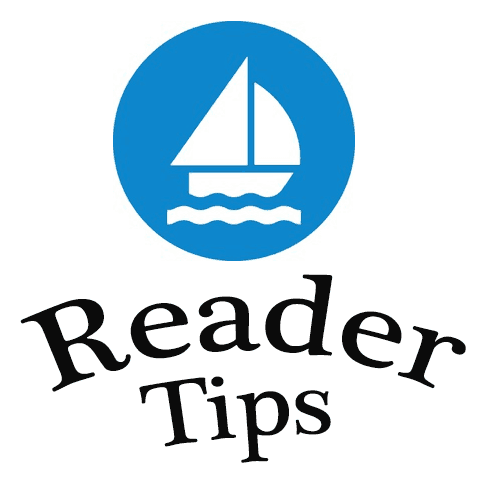
Tony – Wooden Boat Builder from São Paulo, Brazil. “I asked for samples from 3 major manufacturers here in Brazil. My testing involved boiling for 3 hours – 4 times. Between boiling sessions, samples were frozen for one night.
Tertius – Wooden Boat Builder from Knysna, Western Cape I also switched to exterior grade after faults in BS1088 grade. But yes…boil it a couple off times and look carefully for voids and overlaps.
It’s easier being a boatbuilder to fix and make an informative decision. After all, how long do I want it to last! A friend of mine used exterior grade pine ply. He took it for pressurised Tanalith treatment. Any faults in the board made it explode.
James Draper – Sanderscore Craftsman The preparation of Plywood surfaces is often key to the longevity of the plywood. By sanding and properly prepping a piece of marine plywood, the substrate stands a better chance of surviving the often harsh conditions of the marine environment. Protect the wood with suitable marine quality paint, but don’t skip on the preparation, keying the surface is fundamental.
Robert from Portland, Connecticut, US – You can use resin thinned down with acetone so that it becomes very watery seeping deep into the pores of the wood and sealing them. Then lightly sand and repeat until the wood grains are filled with the resin. Coating plywood like this will keep water from being able to enter. This is a trick used by manufactures to seal plywood that works quite well.
Any questions then feel free to get in touch ?
Where can I buy it in Co. Galway
About 25 years ago I thought I would build a broadbill duck hunting boat. So I did.
Using marine plywood. I still have the boat but is in rough condition not keeping up with repairs as needed.
One thing I have learned in my 67 years is that all things expand and contract at different rates.
Wood and fiberglass in hot summers and frozen cold winters.
Once a crack develops all he’ll breaks loose.
i HAVE REBUILT THE WOODEN CACIN ON MY 21′ FISHING BOAT, USING “MARINE PLY”. BUT AFTER ONLY A COUPLE OF WEEKS THE PLY IS GOING BLACK IN PATCHES EVEN THOUGH I TREATED THE CUT ENDS ETC WITH LINSEED OIL AND VARNISHED OVER, IT’S DRIVING ME MAD.
Good side up or down?
A good all round summary. but let me warn everyone. Most hardwood marineply that is manufactured in asia fails. I.E. it delaminates, mostly in the centre of the sheet, so you don’t find it untill it becomes a big problem. It is also very heavy and dense and is not terribly successful when trying to get a good bond with fibreglass sheathing. be it epoxy, Vinylester or polyester resin being used. Here in Australia there is a lot of Malaysian hardwood marineply being sold with the BS 1088 certification on it that falls to bits. We call it the Bull Shit 1088 marine ply. so my advice would be to buy a good Quality Hoop pine or maple marine ply, pay the extra for Gaboon ( light weight ), and avoid the cheap hardwood imports.I have been building high speed laminated (cold moulded ) timber planing craft for the past 45 years and have a reasonable knowledge on the subject.
Any referral to a better ply dealer
May be you should try and go check the marine plywood produced by SMIP-Dragonbrand, I think you won’t find that problems again.
thanks Graeme, where can i buy the good quality marine plywood for my boat flooring? i have an area of 2400×2400 on the cabin deck that i am replacing. i live in Sydney and please help me make contact with the right supplier.
Nice article, only I have built plywood boats up to 60 ft, using only quality untreated plywood, these boats are coast Guard approved as commercial passenger use, just prep it by grinding the waxy outer layer and glue it up, my boats were built in the 80s and still alive today, running tours in Hawaii, Florida, Virginia islands, Bahamas,
I agree with you William Austin A good quality softer wood marine ply can be prepped with a coarse sanding before the glassing but a dense hardwood ply is no where near as successfull.
Especially with west system epoxy warmned up to lower it’s viscous state so it permeates the substrate using extra slow hardener for maximum penetration.
We use an epoxy with an open time of 9 hours when we have a heavy laminate to get together in one hit. gives you time to have lunch half way through the job.
Well I have finally encountered another boater that knows what the he’ll he’s talking about , ….keep it up Graeme there’s a lot of misinformation going on out there
I’m under the impression Marine Grade Plywood used to require it be 100% free of voids, but I read a while back that standard was lowered to 80% void free. Does this jive with what you all are seeing when you buy sheets of it? Just wondering why the change?
you have to think carefully about what you are using the ply for. some things to consider: 1. it is untreated timber, so you must seal it VERY well or it will rot out real quick. 2. Every time I have lifted glass from a ply deck or cabin more than 10 years old, there has been a disconcerting amount of mush in there, coming from delaminations in stressed areas like around winches and cleats, also fastening holes, etc. 3. The laminations in marine grade ply are very thin particularly when you start getting down around 6mm, so consider how they will wear. 4. I know a lot of builders who are moving to heavily treated exterior grade construction ply for decks, or deck underlays etc which will be exposed to rain, and is a lot more resilient to fresh water and the problems it brings (remember salt water in the bilge is a good thing for planked boats, but it still condenses fresh!). Marine grade ply does however bring good strength and dimensional stability, so great for hulls. However I’ve seen good results with plain old exterior grade H- series treated timber. 5. Anyone can put a BS 1088 stamp on something, as it isn’t a proper standard any more, it’s basically just there for show: BS being the operative part of that equation! I’ve had stuff with that stamp delaminate almost immediately – even under white “marine grade” paint.
The main advantages of marine plywood are only utilized IF (!) the epoxied glass cloth is cracked, that means the epoxy soaked plywood AND the glass cloth AND the fill coat are all cracked. And what are the chances this will happen without the user fixing it before any internal damage appears ? VERY VERY SLIM CHANCE. And to support my opinion: Strip built kayaks and boats are not built with “Marine wood”, they are built with any wood, and the strips are glued with regular carpenters’ glue (and not any fancy “marine” glue). The strength comes from epoxy/glass encapsulation which also seals the wood. Stitch and Glue kayaks can be built with regular good quality plywood (not “marine”) and they will be wonderful long lasting boats. I built my 1st Stitch and Glue kayak using BS-1088 plywood because that’s what everybody are doing. I now know better and on my next boat I will save $$$ with regular good quality plywood.
My only issue with this post is that it is too optimistic about “real” marine plywood (BS1088 or better). While BS1088 requires high-quality wood and heat-resistant glues, it is still WOOD. As such, it MUST be protected from water intrusion. Real marine ply resists rot only very slightly better than the cheapest stuff in your local lumberyard. It’s benefits are in strength (no voids, many more plys at a given thickness, and for some types, lighter weight). No matter what wood you use in a boat, you must either do it the old way (use more and thicker wood so that even after it is half-rotted it is still strong enough to function as a boat (not really recommended except for historical restorations); or SEAL the WOOD completely! I have restored 12 boats (including my own), and have built 3 small boats. I strongly suggest Encapsulating (developing a total seal) rather than just Coating (slapping on some epoxy). I use three coats of good epoxy on ALL endgrain (Any cut in plywood is endgrain). I use at least two coats on all other surfaces. Note that one should apply 2nd and later layers between “fingerprint and fingernail” so that you end up with a chemical bond between All layers (creating one solid piece) rather than just separate coats, one over the other. Yes, I always use fiberglass or xynole polyester. Enough ranting, hope this is useful. ( BTW: “Fingerprint” occurs early in the cure process… it is when you can firmly touch the epoxy and leave a fingerprint, but it does Not stick to your finger. “Fingernail” occurs later in the process and means the point where you can still barely indent the curing epoxy with a fingernail but cannot break through.)
Very good commentary, especially liked the fingerprint fingernail test. What i think is missed by a lot of people is that the raw materials the plywoods are made of have deteriorated significantly over the years. 40 years ago a BS 1088 sheet would probably have been fabricated in an established plywood plant using old growth woods for the plywood layers. Today most of those plants are out of business and most of the raw materials are less than 20 years old. That tropical hardwood core will come from an immature tree and as such has not the longevity or rot resistance of a mature tree
Thanks for the comment Sam, some really interesting points to consider. Due to a lack of good affordable sources for marine plywoood i’m now using composite sheeting that I laminate myself with really good results.
boats in general, and more so with pontoon boats, there are only so many ways to build a boat, and very few material choices.
the big differences tend to be in floor layouts, how the interior or the deck is laid out. what type of seats, and where are they.
and in what powers it, which can be different between two of the same make, model and year depending on what the dealership that sold it dealt with.
mercury is the most common one, having more sales then anybody else has that effect.
but even if two of same make, model and year both have the same brand powering it, the hull may be rated for 90 hp and one of them the person buying it paid for the 90 hp while the other one only got the cheaper 60 hp.
What’s the best way to prep a pontoon floor (plywood of course) in order to lay peel & stick closed-cell foam pads such as SeaDeck?
Thanks for explaining how fiberglass in wood can easily support the weight of a person. I’d like to get some wood for a project I am planning. I’ll see what I can do about using fiberglass wood.
Thank you for the info for which I was looking for answers as I shall be repairing my fiberglass boat soon.
I researched some marine plywood suppliers around and the best wood sort available here seem to be the ones with birch wood imported from Russia/Ukraine and the beech wood from Türkiye. Both plywoods are manufactured locally and my reference producer seems to have good reputation (I used another product of them and was very content).
Similar to your Jewsons case, though both are named “marine”, for some reason only the Beech is specked for boat use and the birch is not (the “boat” is simply missing. Not sure if accidental omission).
When I check their data on pressure resistance, bending resistance, cutting resistance, density etc, Birch seems to be faring better.
Any experiences with either sort of wood in boat use?
Thanks
Forgot to mention. Both plywood sorts are produced locally in Türkiye, for that reason I mentioned no brands.
Good side up or down?
Cost of 6 sheets of marine plyboard for my pontoon boat.